Technology
Wheels
Seismic wheels are made in the USA at the world’s most advanced urethane wheel factory, headed by the field’s greatest engineering mind. With over 40 years’ experience, “Nealo” is responsible for the vast majority of significant advances in modern urethane wheel tech. Since 2005 Seismic has worked with this manufacturing leader – more closely than any other skateboard brand – to develop and refine progressive wheel shapes, hub profiles, and urethane formulas that keep pace with the ever-evolving performance requirements of all the many different skating disciplines. The two companies have also collaborated on advanced wheel performance testing research, in cooperation with a leading university engineering department.
Most skateboard wheels are made from only two basic chemical ingredients to form a simple urethane brew with limited performance characteristics. But as many as nine distinct chemical materials, all sourced from the finest international suppliers, are meticulously combined in each unique, state-of-the-art Seismic formulation – always developed through extensive R&D and rigorous double-blind testing by elite skaters in carefully-controlled conditions. Coupled with stringently-controlled factory processing (perfectly homogeneous mixing and precisely-timed catalyzation), the result is urethane that dramatically out-performs the competition.
Seismic produced its first wheel in the middle 1990s – a 66mm cruiser assembled with Seismic trucks on “Richter 7.1” completes, featuring slalom decks hand-built on special commission by the legendary Bob Turner. Like the rollout of the original Seismic spring truck in 1994, this plan was years ahead of its time.
In 2004 Seismic took over the 3DM line and began offering high-performance wheels on a larger scale. The original 3DM Cambria, Avalon and Avila shapes utterly dominated international slalom racing for years. They’re still used by elite racers, cruisers and carvers around the world. Since 2005 Seismic has developed more advanced wheels under the flagship Seismic brand – including shapes that have helped win numerous World Championship titles in both Slalom and Downhill racing, and shapes that have helped set multiple speed records including the standing Guinness World Record for downhill speed (Pete Connolly, 91.17 mph / 146.73 kph, set Sept. 16, 2017, at The Top Speed Challenge in Quebec, Canada).
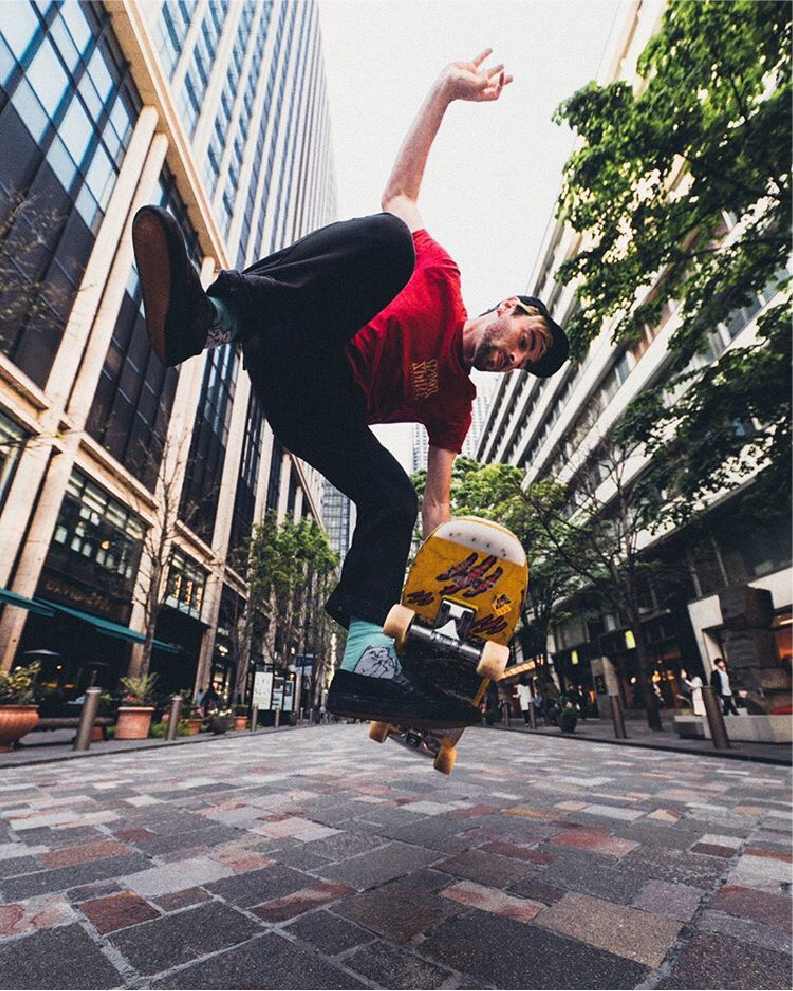
Bearings
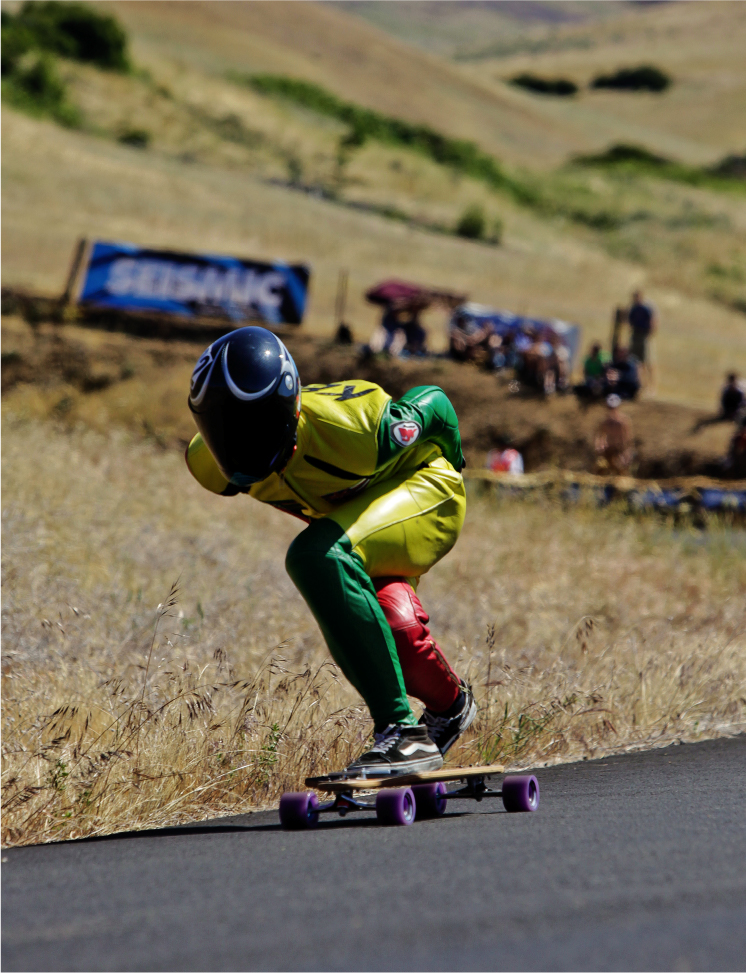
Breakthrough self-aligning design corrects for flaws in bearing seat levelness, bearing seat spacing, axle diameter and axle straightness.
More than two years in development, Seismic Tekton™ bearings feature wide, flat contact surfaces at the ends of integrated, custom-machined half-spacers. The broad flanges square up, co-align and self-stabilize inside your wheels – correcting for flaws in bearing seat levelness, bearing seat spacing, axle diameter and axle straightness.
The Tektons literally block themselves from sitting or rocking out of alignment, so they stay straighter than any other bearing system ever. Your wheels roll faster with better control, while the bearings last longer and stay quieter. Other features include: steel balls, nylon retainers, black outer casing, removable rubber-coated steel seals with printed graphic, and a proprietary lubricant combining both oil and grease.
The inner race is stepped underneath the seal to resist contamination, and it’s stepped between the bearing and the flange to save weight. On the side opposite the flange, the inner race extends 0.5mm to form a thin integrated washer. No bearing spacers, axle washers, or World Record budgets required!
Trucks
In 1993, Seismic patented one of the most original and sophisticated technologies ever developed for skateboarding. The first of the new generation of longboard trucks, it was so far ahead of its time that even we had to poke fun at it in our September 1994 TransWorld Skateboarding ad! But soon enough, our spring-loaded design inspired cheap imitations in off-road skateboards and surfing cross-trainers.
Redesigned in 2003 and again in 2015, the Seismic spring truck technology now offers impressive tuning options for the discerning skater, and advanced performance for longboarding, racing, all-purpose cruising, Old School park/pool styling, and snow/surf cross-training.
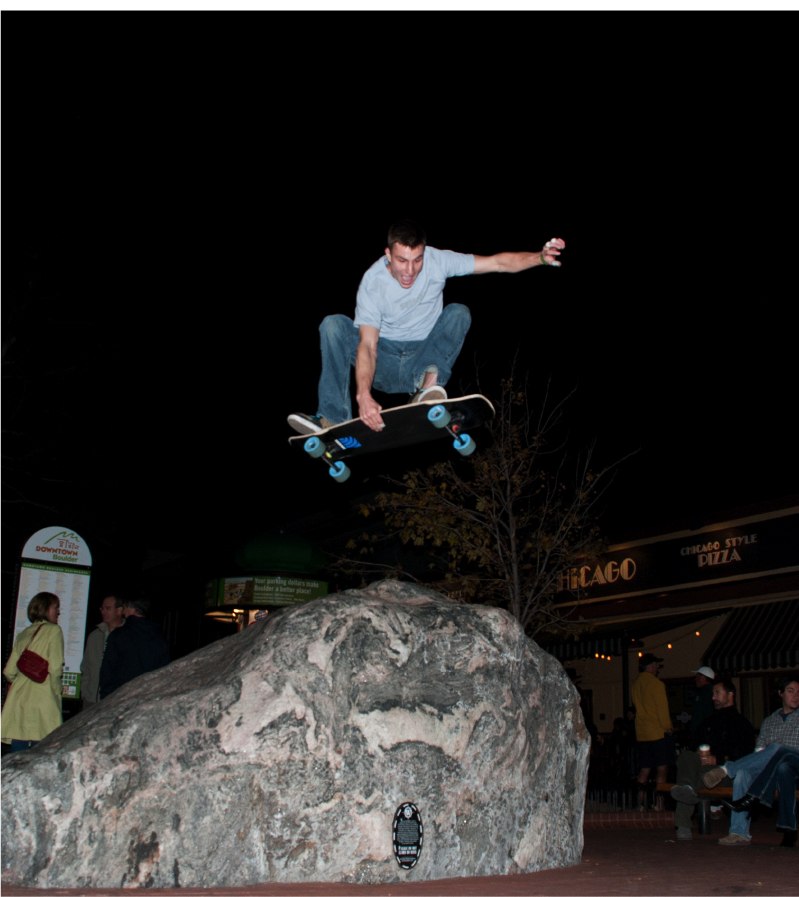
Grip Tape
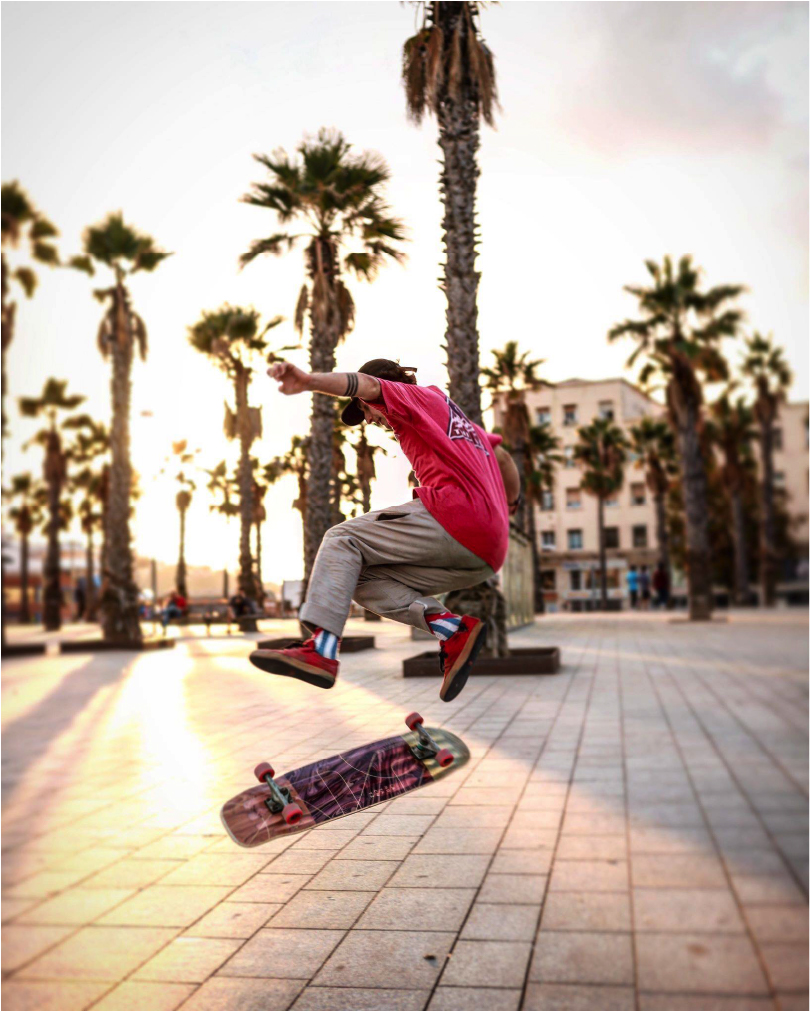
Noticeably sharper, tougher, and grippier. Grit stays ultra-sharp, doesn’t flake off. No smearing or peeling, even in heat or rain. The best grip in the history of grip.
The PSA (pressure-sensitive adhesive) on the back of Lokton is some of the best, most heat-resistant on the market.
36-grit Coarse or 60-grit Medium – Just as durable as the original 36-grit version, but with finer granules for easier footing adjustments and less wear-and-tear on shoes.
Available in four (4) laser-cut patterns, as well as Solid for maximum surface coverage. Fishnet (new!), Honeycomb, Metal-Plate, and Ninja Star hole patterns decrease weight by up to 40%, while hole edges increase grip.
Boards
Meticulously developed over years of prototyping and testing, Seismic boards offer something for everyone – from good-time cruisers, cross-campus commuters and longboard freestylers, to competitive racers and fearless freeriders. Constructed with varying blends of maple, bamboo, black walnut, oak, fiberglass, and carbon, all bonded with the most advanced epoxy. Most models pre-gripped with unique and highly-functional laser-cut patterns.
Completes assembled with components featuring the most innovative engineering in their class: Seismic wheels with unmatched speed, grip and slide characteristics; Tekton bearings with world-record speed and patented self-alignment system; and Aeon trucks with patented internal cylindrical bearing for smoother, truer turning through a deeper range of lean.
Redesigned in 2003 and again in 2015, the Seismic spring truck technology now offers impressive tuning options for the discerning skater, and advanced performance for longboarding, racing, all-purpose cruising, Old School park/pool styling, and snow/surf cross-training.
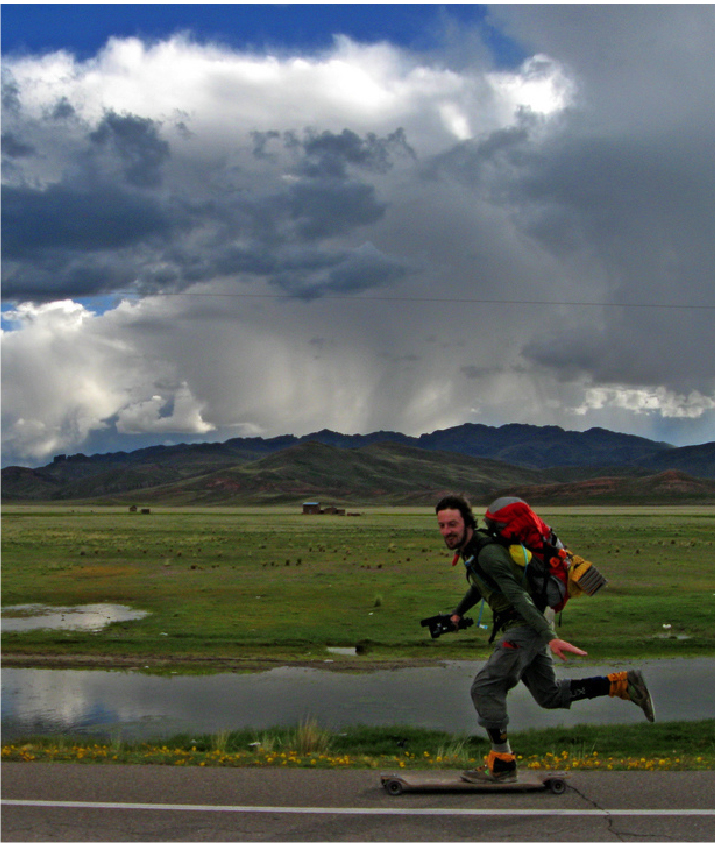